Challenge
Bolted connections in the wind industry have a history of failure and are subjected to huge dynamic loading so require regular inspection to ensure they are mechanically integral. Whilst the inspection regime varies between turbines OEMs, it typically consists of a torque, tension or UT check on 10% of critical bolted connections on a yearly basis. The existing inspection regime represents the costliest planned maintenance activity, consuming approximately 30% of the annual maintenance budget.
On top of this, bolt inspection presents significant health & safety risks for technicians as a result of using heavy and cumbersome equipment, and working at height. Some Operators have reported that almost 5% of technicians will have an accident or near-miss every year.
The challenging bolted connections in the Wind industry include:
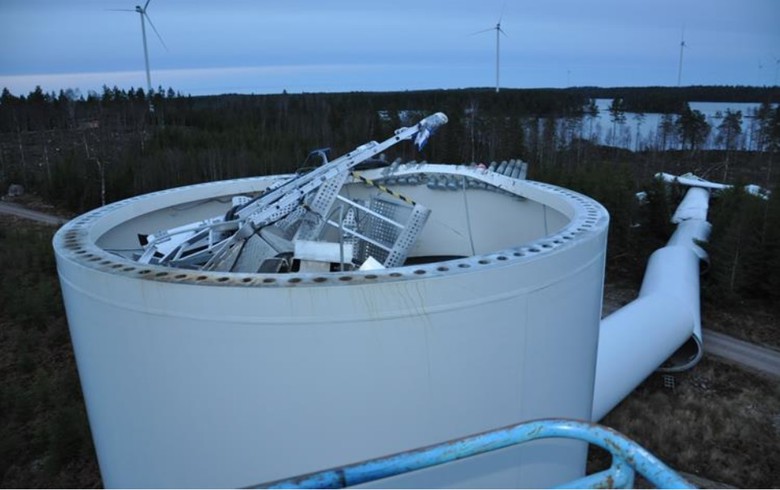
Solution
Through the deployment of InterBolt technology, Operators will have access to bolt load measurements remotely through the InterBolt Cloud platform. When a loose bolt is detected, an alert will be generated and the Operator can take the appropriate action to ensure the fault is rectified in the most cost efficient manner whilst still ensuring the asset operates reliably.
When technicians need to install bolts or retighten them, they can use the onsite monitoring functionality of InterBolt to quickly verify the bolt load. This means technicians don’t need to transport and use heavy and cumbersome equipment which reduces H&S risks.
Whilst a typical turbine will have up to 1000 critical bolted connections, a 10-20% roll out of InterBolt technology gives a sufficient dataset for Operators to implement a risk-based maintenance regime.
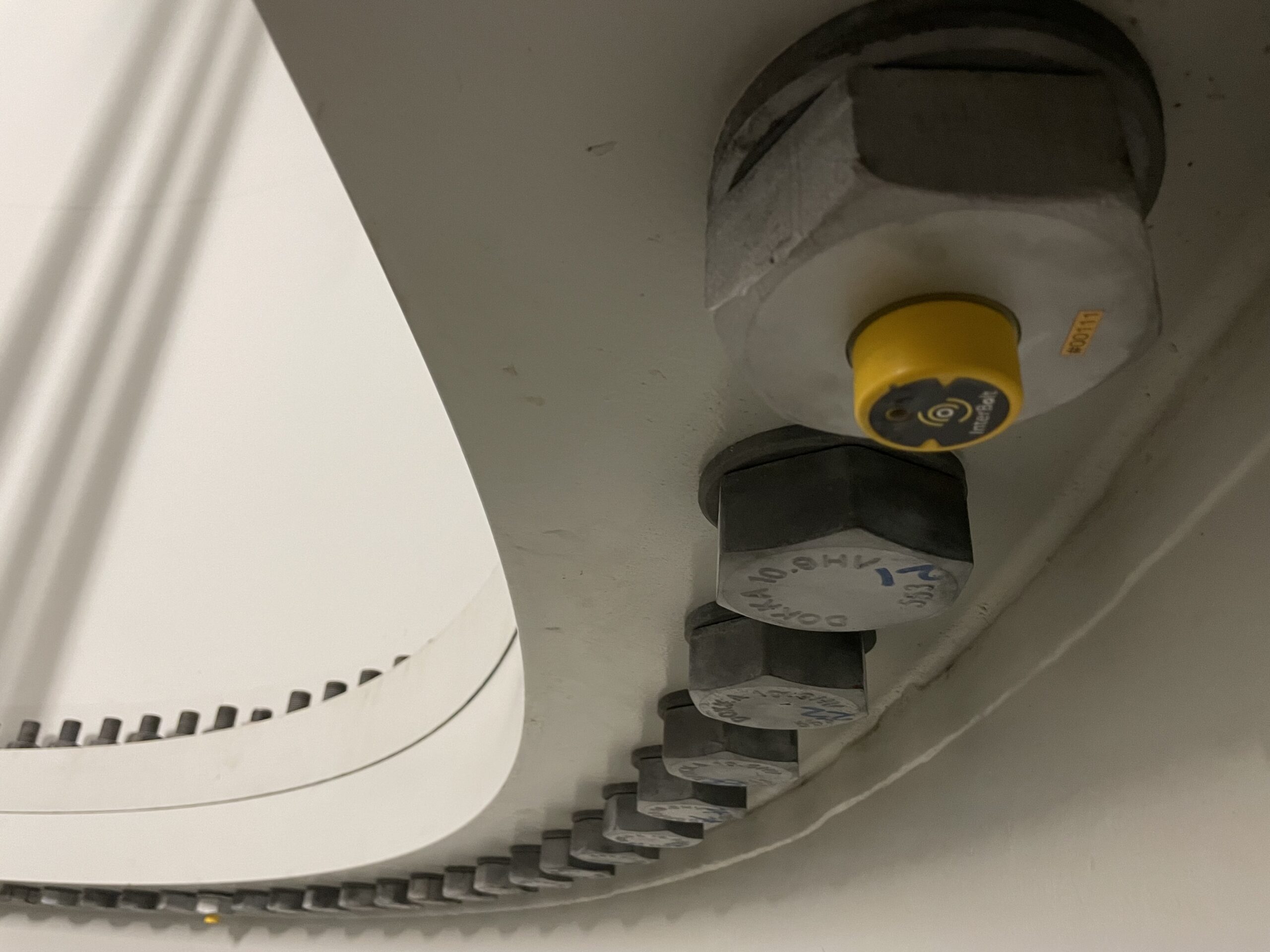
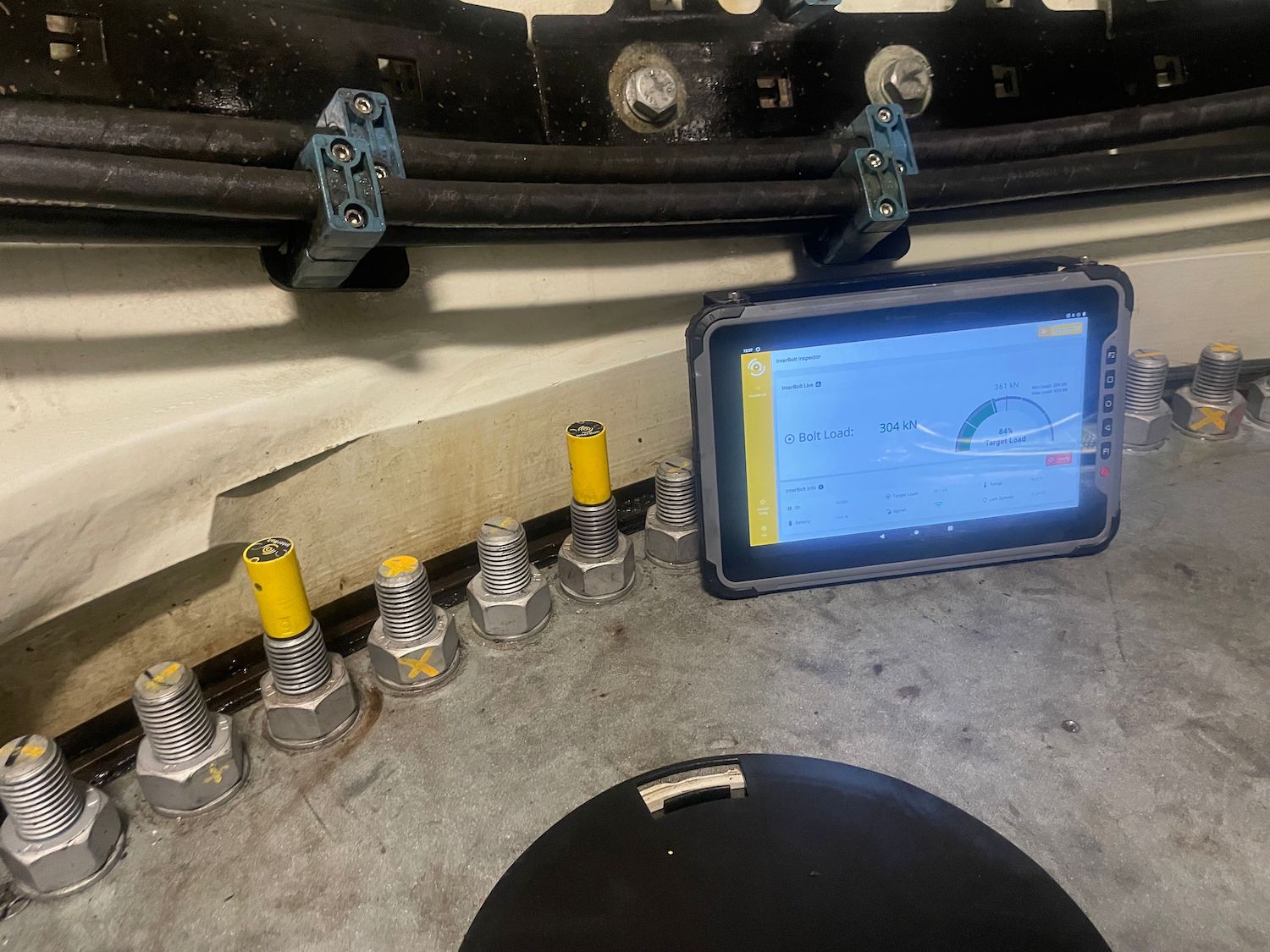
Value
Through adopting the InterBolt solution, Operators can eliminate the need for periodic manual inspection of bolted connection on wind turbines. This can:
-
Reduce bolt inspection costs by up to 90%, significantly reducing the cost of delivering wind energy.
-
Minimise H&S risks for technicians through reducing onsite work and removing the need for using heavy and cumbersome equipment to check bolt tightness.
-
Eliminate the need for asset downtime for bolt inspection, minimising lost production costs.
Case study
As part of a funded project through the Offshore Wind Growth Partnership, the largest deployment of bolt load monitoring technology was deployed on the Offshore Renewable Energy Catapult’s Levenmouth Demonstration Turbine.
Using the embedded LEDs on the InterBolts and the InterBolt Tablet app, the technicians were able to confirm that they tightened the bolts to a correct preload. The need for the typical 500hr check back was then eliminating because technicians were able to confirm minimal preload losses through the InterBolt Cloud platform.
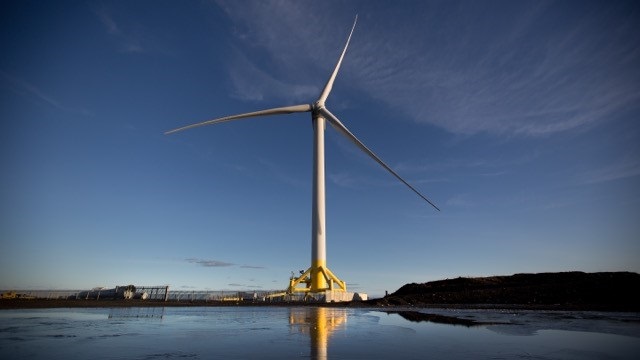
Live data access
Below is a link to the InterBolt Cloud platform for a live installation on the Offshore Renewable Energy Catapult’s Levenmouth Demonstration Turbine, funded through a project with the Offshore Wind Growth Partnership.
Site: dashboard.interbolt.co.uk/
Email: demo@interbolt.co.uk
Password: Intelligentbolting