Challenge
Bolted connections in the rail industry are subjected to some of the harshest operating conditions particularly from a vibration and shock perspective, with infrastructure-based bolts seeing accelerations up to 1000g routinely. This can lead to vibration induced loosening which can lead to service affecting failures and at a very worst case, can cause catastrophic accidents such as the Grayrigg derailment in 2007.
With a clear focus on maintenance modernisation, the rail industry is looking to improve the reliability of their infrastructure whilst minimising the H&S risks of technicians through initiatives such as ‘Boots off ballast’ and eliminating red zone working.
There are a huge range of challenging applications in the rail industry, particularly on infrastructure and rolling stock where the fasteners are subjected to dynamic loading and vibration. Applications include:
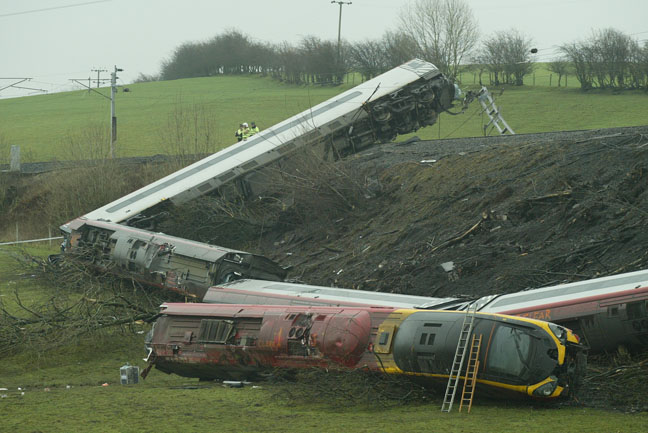
Solution
With InterBolt technology, technicians can accurately and repeatably tighten critical bolted connections to their designed preload. When bolts are tightened to their target bolt load, they are more resilient to in-service failure, thereby increasing their operational life.
Post installation, technicians can remotely monitor the tightness of the fasteners without having to walk the track. This significantly reduces the time that technicians need to be on site and exposed to the risks of a live railway environment. When a loose bolt is detected, the maintenance teams will be alerted to this and they can take the appropriate action to minimise the impact on running services, whilst still ensuring the infrastructure is safe.
Outside of wide scale roll-out of InterBolt technology, it is also widely used to validate changes to installation procedures and components in the bolted connection. Through small scale deployments, any modification can be empirically proven and meta data for risk based maintenance regimes can be generated.
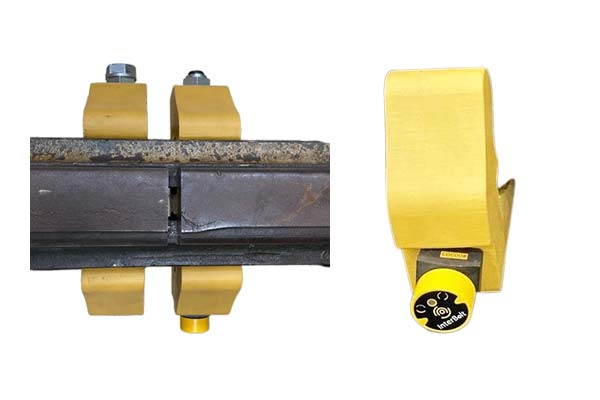
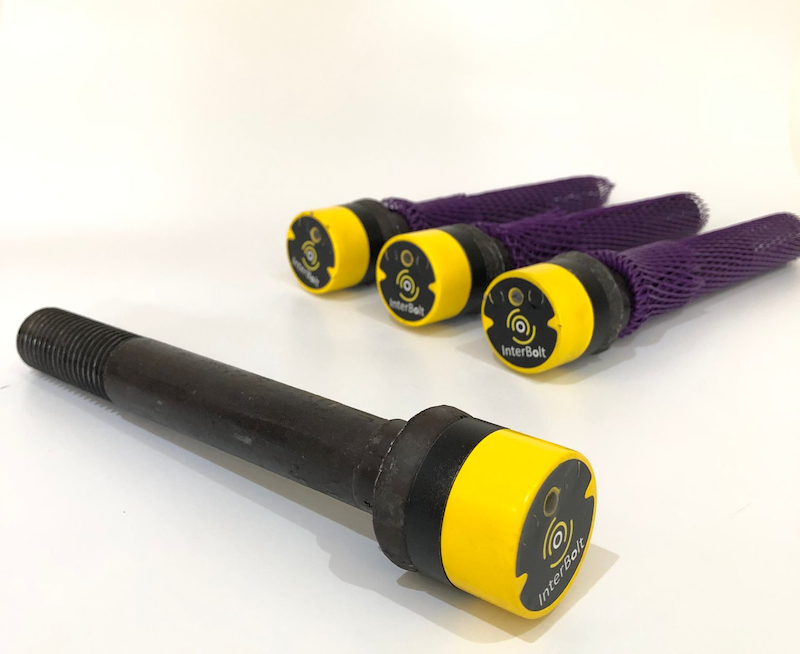
Value
Through deploying InterBolt technology, Operators can:
-
Improve asset reliability. Through ensuring bolts are tightened correctly, the operational life of the connection can be maximised.
-
Minimise H&S risks for technicians. Through eliminating the need to conduct track walks to periodically check the tightness of critical bolts, the amount of work technicians need to do on site is reduced, minimising the time they are exposed to the risks of a live railway environment.
-
Empirically validate changes to procedures and components in the bolted connection.
Case study
Through our collaboration with Tracksure, InterBolt has been deployed across hydraulic brake retarders. The bolted connections of these assets have a long history of failure due to high dynamic loading, shock and soft members in the connection.
For this application, the technicians were able to validate the bolt load at installation using the embedded LEDs and through connectivity with the InterBolt Tablet. This ensured that bolts were accurately tightened to the designed preload even when they were using torque-based tightening techniques and it was difficult to control thread and under head friction.
Post installation, the Operations team used to InterBolt Cloud platform to remotely monitor the bolt load. Their time-based maintenance regime which required a daily track walk was replaced with a condition-based regime whereby they only sent technicians to site once a loose bolt was detected. This enabled them to reduce time on site by over 90%.
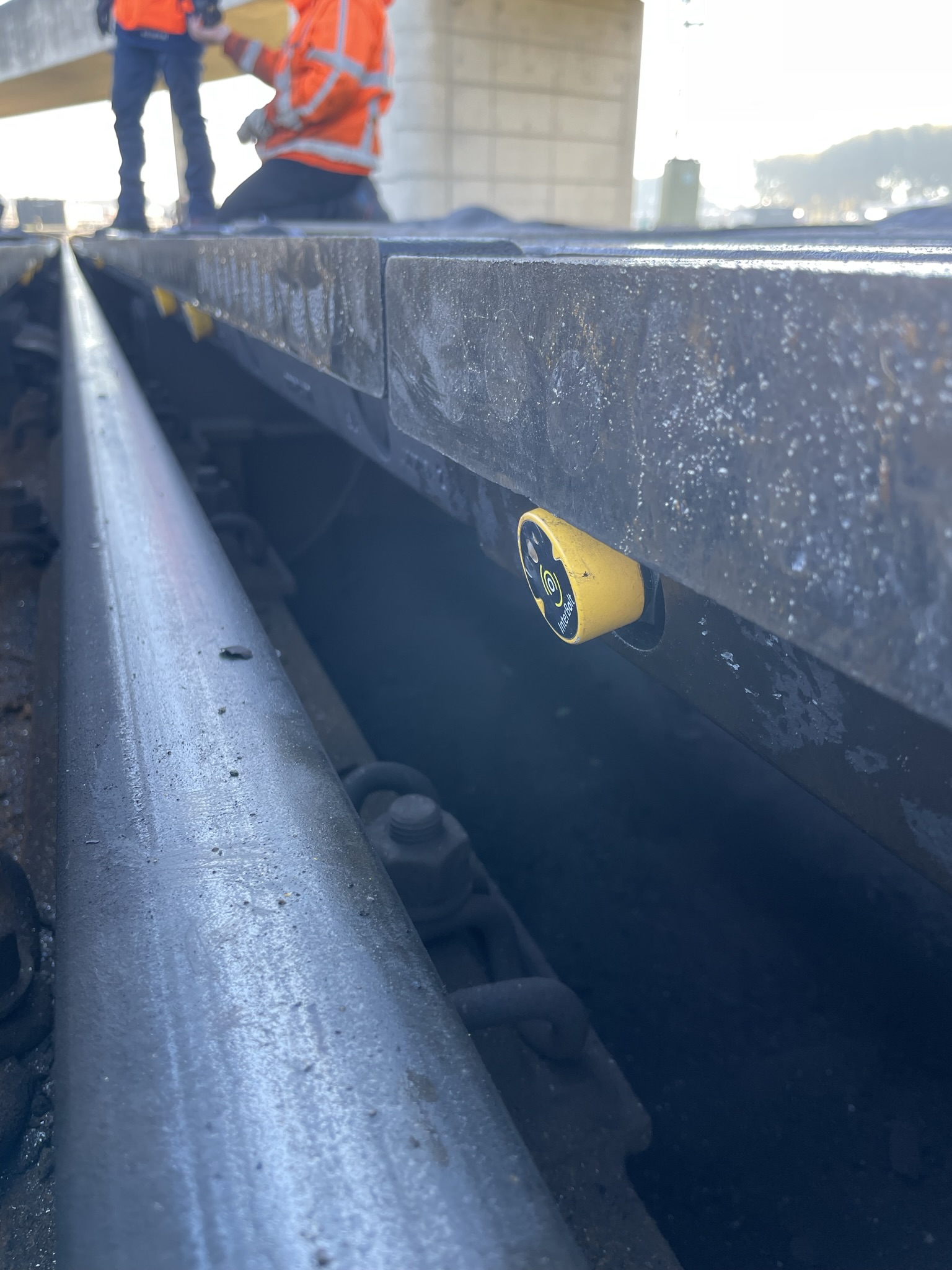